TM 10-3510-209-10
2-4. GENERAL MAINTENANCE PROCEDURES .
As you perform your PMCS, keep in mind the following:
a.
Cleanness. Dirt, grease, oil, and debris only get in the way and may cover up a serious problem.
b.
Bolts, Nuts, and Screws. Check them all for obvious looseness and missing, bent, or broken
condition. You cannot try them all with a tool, of course, but look for chipped paint, bare metal, or
rust around bolt heads. If you find one you think is loose, report it to your supervisor.
c.
Welds. Look for loose or chipped paint, rust, or gaps where parts are welded together. If you find
a bad weld, report it to your supervisor.
d.
Electrical Wires and Connections. Look for cracked or broken insulation, bare wires, and loose or
broken connectors. Tighten loose connections and make sure the wires are in good condition. If
you find a bad wire or connector, report it to your supervisor.
e.
Water Lines and Fittings. Look for wear, damage, and leaks. Make sure clamps and fittings are
tight. Wet spots show leaks, but a stain around a fitting or connector can mean a leak. If a leak
comes from a loose fitting or connector, or if something is broken or worn out, report it to your
supervisor.
2-5. OPERATOR/CREW PREVENTIVE MAINTENANCE CHECKS AND SERVICES TABLE.
a.
See table 2-1 for operator preventive maintenance checks and services (PMCS).
b.
Refer to TM 5-6115-585-12, Generator Set, Diesel Engine Driven, 10 kW, 60 Hz, for operator
preventive maintenance checks and services (PMCS) for the generator set.
c.
Refer to TM 9-2330-376-14&P for operator preventive maintenance checks and services (PMCS)
for the laundry unit trailer.
d.
The Daily Walk-Around PMCS Routing Diagram will be of help to complete B, D, A, or W PMCS.
It shows laundry unit PMCS routing track which matches the sequence of PMCS to be performed.
2-16
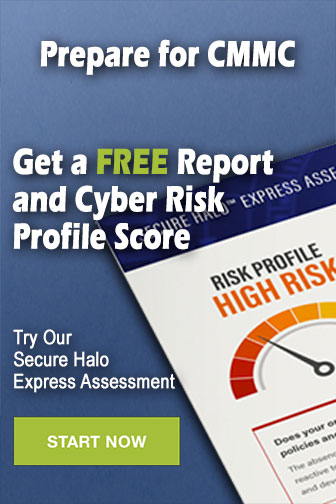