TM 10-3510-220-24
2-12. GENERAL (CONT)
4. Splicing Wires. To repair broken or cut wires that are otherwise sound, the mating ends can
be stripped and spliced. A commercial butt spice can be crimped onto the ends to join them,
or a Western Union wire splice can be made. The latter is made by stripping 1/4 - 1/2 inch
(6.5 - 12.7 mm) of insulation from the wire ends, holding the ends parallel and facing
opposite directions, then twisting each end around the other wire at least three turns.
Solder and apply insulation as described above.
5. Crimping Terminals. To install a terminal on the end of a wire, strip 1/4 - 1/2 inch (6.5 - 12.7
mm) of insulation from the end of the wire, apply a one inch piece of heat-shrinking tubing
(if the terminals are of the uninsulated type) and insert wire end into the shank of the
terminal. Crimp the shank, and install heat-shrink tubing, if necessary.
b.
Cleaning and Inspection of Antifriction Bearings. Refer to TM 9-214, Inspection, Care, and
Maintenance of Antifriction Bearings.
c.
Cleaning and Inspection of Mechanical Parts.
(1)
(2)
(3)
WARNING
Drycleaning solvent P-D-680 is toxic and flammable. Wear protective
goggles and gloves and use only in well-ventilated area. Avoid contact
with skin, eyes, and clothes and dont breathe vapors. Do not use near
open flame or excessive heat. The flash point is 100 - 138°F (38 - 59oC).
If you become dizzy while using cleaning solvent, get fresh air
immediately and get medical aid. If contact with eyes is made, wash
your eyes with water and get medical aid immediately.
WARNING
Compressed air used for cleaning purposes will not exceed 30 psi (kPa).
Use only with effective chip-guarding and personal-protective
equipment (goggles, shield, gloves, etc.).
Clean metal parts in drycleaning solvent (Item 10, App C). Thoroughly dry the parts with
compressed air, observing all safety precautions.
Fibrous or rubber parts can generally be cleaned with warm, soapy water and dried with
compressed air.
Inspect metal parts for cracks, breaks, bends, worn edges, and rough bearing surfaces.
Damage that alters the part or its function is cause for replacement of that part.
d.
General Repair.
(1)
(2)
(3)
Repair the laundry unit to normal operating condition by replacing or repairing a defective
component and/or by needed adjustments.
Cleaning and lubrication is sometimes all that is needed to return an item to operating
condition.
Remove and replace only those items necessary to make repairs. After replacing the
defective components, ensure that the laundry operates correctly by making a visual
inspection and by performing an operational check. Refer to TM 10-3510-220-10.
2-44
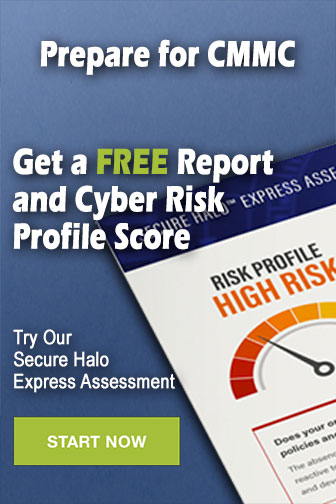