TM 10--3510--221--24
0003 00--4
WASHING/DRYING SYSTEM THEORY
OF OPERATION -- Continued
0003 00
SECOND--STAGE RINSING -- Continued
At this time the control system increases the drive motor speed until the basket is rotating at high extract speed
(approximately 600 RPM). The basket remains at extract speed for approximately seven minutes while the drum is
drained. At the end of extract the control system turns off the drive motor and water pump, applies the brake, and
closes ball valves (FV102 and FV107). For the second--stage rinsing process the operator has the option of selecting
a formula that calls for sanitizer or Finish Reapplication System (FRS) application. When these formulas are selected
the operator will be notified by the control system when it is time to add sanitizer or FRS. The operator adds the
sanitizer or FRS through a sluice located on the front of the drum. The sluice can also be used to add detergent in the
event of a detergent pump failure.
DRYING
The control system provides a signal to start drive motor (M100) and blower (M104). The control system also opens
outlet damper (FV110) and closes inlet damper (FV111). The basket starts rotating at tumble speed. As the basket
tumbles ambient air is drawn through a heat exchanger connected to the LADS heating system. The hot air passing
through the heat exchanger is then directed into the drum inlet. As the air enters the drum it passes through the
laundry removing moisture. The air is then exhausted out of the blower. While the air is circulating through the drum,
temperature sensors (TE101 and TE102) monitor the temperature at the drum inlet and outlet. Once the air outlet
temperature reaches the formula specified drying temperature the control system will maintain the proper inlet
temperature by opening and closing the inlet damper. This allows for accurate air temperature control regardless of
the ambient temperature conditions and drying temperature selected. While the laundry is drying the basket tumbles
for approximately thirty minutes. Near the end of the drying cycle the control system opens inlet damper (FV111) for
approximately one minute to allow ambient air to circulate through the drum. This cools down the laundry so that it
can be safely handled by the operator. At the end of the drying cycle the control system turns off the drive motor and
blower and applies the brake. The control system also closes outlet and inlet dampers (FV110 and FV111), retracts
the door lock (DN100), and provides a signal to the operator panel that the laundry cycle is completed. The operator
then opens the front door, removes the laundry, and repeats the process.
DRUM SUPPORT/VIBRATION DAMPENING
Before power is applied to the LADS the drum rests on the ISO frame structure. In the operational mode the air
system pressurizes four air bags that inflate to support the weight of the drum. Leveling valves connected to the front
two air bag mounts are used to adjust the pressure in the air bags. This allows for side--to--side leveling of the drum
when the LADS is located on uneven terrain. Four shock absorbers, located at each corner of the drum, are used to
restrain the drum while it is rotating. Vibration eliminators are also located on the sides and back of the drum mounts
to dampen the amount of vibration that is transferred to the LADS structure during the extraction steps.
DRUM ROTATION
The drum basket is driven by an electric motor (M100) connect via a drive belt and two sheaves. During a laundry
cycle the control system changes the speed of the motor to achieve the proper basket rotational speed and direction
needed for tumble and extract. A cooling fan (M106) is used to continuously direct fresh air onto the drive motor to
prevent the motor from overheating. A proximity sensor (ZS102) monitors rotation of the drum sheave and provides a
signal to the control system verifying the drum basket is either rotating or stopped.
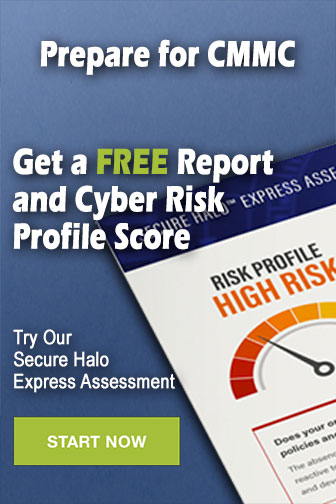