TM 10--3510--221--24
0004 00--1
WATER RECYCLE SYSTEM
THEORY OF OPERATION
0004 00
WATER RECYCLE SYSTEM
The water recycle system takes the dirty wash water from the drums and recycles the water for use during the
second--stage rinse process. During start--up of the LADS the water recycle system also provides steam that is used
to heat up the rinse 2 water. Water recycle system operation consists of the following sub--operations.
WATER DISTILLATION
A still is used to distill the dirty wash water. The still contains fourteen heatplates that have hot thermal fluid (from the
heating system) circulating through them. When dirty water is dumped into the still it heats up and begins to boil. The
solid materials in the water such as dirt and sand collect in the bottom of the still while the water turns into steam and
exits through the top of the still. Connected to the still are several monitoring and safety devices. Temperature sensor
(TE200) monitors the temperature of the steam exiting the still. Pressure sensor (PT200) continuously monitors the
still internal pressure. If the pressure rises to an unsafe level a signal sent to the control system by the sensor will
prompt the heating system to turn off. A relief valve is mounted on the still to prevent it from over--pressurizing in the
event of a pressure sensor or control system failure. Level sensor (LT200) monitors the water level inside the still.
During the distillation process foam can be generated from detergent and other contaminates in the water. Excess
foam can cause still pressure to rise to undesirable levels. To prevent excessive foaming an anti--foam solution is
automatically injected into the still from an external container. As wash water is pumped from each laundry drum to
the still the control system turns on the anti--foam pump (M202). Flow switch (FS200), located at the anti--foam pump
outlet, is used to verify that anti--foam is being drawn from the external container. When the correct amount of
anti--foam has been added the control system will turn off the pump. If both laundry drums are ready to drain wash
water to the still at the same time the control system will continue the washing step in one drum until the other drum
has been drained. When the first drum moves to the extraction step the control system will allow the second drum to
drain. This ensures that the proper ratio of anti--foam to water is maintained. Anti--foam solution can also be
manually pumped into still in the event of an anti--foam pump failure. At the end of the daily washing operations
(15--20 laundry cycles) the sludge collected at the bottom of the still and on the heatplates must be clean out. If this
cleaning is not performed the distillation rate will drop causing low water levels in the rinse 2 tank and delays in
starting of further laundry cycles. After the last laundry cycle is completed the operator selects a cooldown sequence.
After level sensor (LT200) signals the control system that the water level in the still is below the heat plates the control
system will turn off the heater. At this time the thermal fluid will to continue to circulate through the dryer heat
exchangers and the still. The control system will turn on the dryer blowers (M104). Ambient air passing through the
dryer heat exchangers will draw the residual heat out of the thermal fluid allowing the still to cooldown. Once the
thermal fluid temperature is below 150 degrees F. The control system will stop thermal fluid circulation and turn off the
dryer blowers. The control system will also release locks (DN200) mounted on the access doors at the back of the
still. The door locks prevent opening of the doors while hot water is present inside the still. Once the still is cleaned
and the doors are closed a position switch (ZS200) mounted on each door will provide a signal to the control system.
The control system will not allow water heating or laundry operations to be started unless the still doors are closed.
Two manual valves are located at the bottom of the still for draining. A vacuum breaker is mounted on the still to
prevent a negative pressure from being generated inside the still during the cooldown sequence.
WATER CONDENSING
The still condenser is used to turn the steam produced by the still back into water. The still condenser consists of four
heat exchangers and a electric motor--driven fan (M200). As steam moves into the coils of the heat exchangers
ambient air passes by the cooling fins. This causes the steam to cool and turn back into liquid. The hot air is then
directed out through the top of the fan. Temperature sensor (TE201), located at the outlet of the condenser, is used to
monitor the temperature of the condensed water. The water exiting the condenser flows to the standpipe. The
standpipe ensures a constant supply of water is available to the distillate pump (M201). As water flows out of the still
condenser it collects in the standpipe. When the water level is near the top of the standpipe a signal from level sensor
(LT201) will cause the control system to turn on the distillate pump.
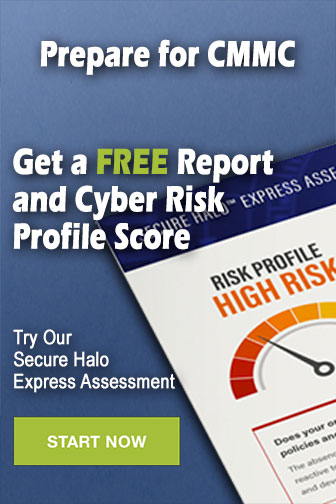