TM 10-3530-207-14
Table 3-1. Operator troubleshooting - continued
MALFUNCTION
TEST OR INSPECTION
CORRECTIVE ACTION
DARNING SEWING MACHINE
Step 4. Check that bobbin case tension is not too tight.
Adjust bobbin case for correct tension (para. 2-12i).
Step 5. Check that bobbin case is not sticky with oil and lint.
If bobbin case is sticky, notify next higher level of maintenance.
Step 6. Check for rough, sharp, or burred edges on rotary-sewing hook, bobbin, and bobbin case.
If defects are found, notify next higher level of maintenance.
Step 7. Check that thread being used is not damp, old, or dried out.
Discard damp, old, or dried out thread. Rewind bobbin with fresh, dry, smooth
thread of the correct weight (paras. 2-12d through 2-12g).
27.
STITCHES SKIP OR FAIL TO LOCK.
NOTE
The most common cause of fail-to-lock or skipped stitches, is using the wrong needle for the
fabric being mended. Always use the correct size, class, and variety needle recommended for
the fabric being worked.
Step 1. Check that needle size, class, and variety is right for the fabric in work.
If needle is incorrect, replace needle with new needle of correct size, class, and
variety (paras. 2-12a and 2-12b).
Step 2. There may not be enough pressure on the presser foot for the fabric being worked.
Vary pressure of presser foot using pressure regulator to try and correct trouble.
Step 3. Check that needle is not blunted or bent.
If blunted or bent, replace needle with a new needle of correct size, class, and variety
(paras. 2-12a and 2-12b).
3-23
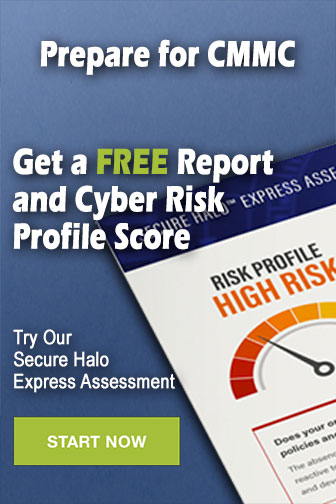