TM 10--3510--221--10
0005 00--3/4 blank
HEATING SYSTEM THEORY
OF OPERATION -- Continued
0005 00
HEATER MONITORING AND CONTROL
An ultra--violet light detector (UV300) is used to continuously monitor the presence of a flame inside the burner
chamber. The signal from the detector is provided to the flame programmer (FP300). During start--up the flame
programmer uses this signal to turn off the ignition transformer. During operation if this signal is not received by the
flame programmer, the flame programmer will stop heater operation, and provide an interlock alarm signal to the
control system.
A pressure switch (PS302) is provided for monitoring pressure at the outlet of the fuel pump. The signal from the
switch is continuously monitored to ensure that adequate fuel pressure is available to support combustion. If sufficient
fuel pressure is not detected the switch will open the flame programmer interlock circuit to stop heater operation.
Alarms signals will also be provided to the control system by the flame programmer and the pressure switch. When
LADS is initially set--up, the heater fuel system must be primed. To prime the system the operator turns on a switch
that connects 110 VAC power to the coil of the burner blower contactor. When the burner blower is operating the fuel
pump is also operating. The operator releases the switch when the lines from the fuel supply are filled and the pump
outlet pressure is high enough to sustain heater operation. A pressure gauge (PI303) is provide to inform the operator
when the fuel system is primed. Pressure gauge (PI304) is provided to aid in troubleshooting fuel pressure problems.
Two pressure switches are provided for monitoring air flow through the burner blower. Pressure switch (PS300)
monitors air pressure at the blower inlet and pressure switch (PS301) monitors air pressure at the blower outlet.
Signals from both switches are continuously monitored to ensure that adequate air flow is provided to support
combustion. If sufficient air flow is not detected one or both switches will open the flame programmer interlock circuit
to stop heater operation. Alarms signals will also be provided to the control system by the flame programmer and the
pressure switch.
Three pressure sensors are used for monitoring the pressure of the thermal fluid. Pressure sensor (PT300) monitors
the thermal fluid pump inlet pressure. Pressure sensor (PT301) monitors the thermal fluid pump outlet pressure.
Pressure sensor (PT302) monitors the thermal fluid heater outlet pressure. Signals from the pressure sensors are
continuously monitored by the control system to ensure the thermal fluid is circulating at the proper flow rate. The
control system will shutoff operation of the heating system if the flow of thermal fluid is not within the required range.
Pressure gauges (PI300, PI301, and PI302) are provided to monitor the thermal fluid pressure to aid in
troubleshooting heating system problems and when servicing the thermal fluid.
Two temperature sensors are provided for monitoring the thermal fluid temperature at the heater outlet. Temperature
sensor (TE300) is used to control operation of the heater and regulate the temperature of the thermal fluid going into
the dryer heaters. When the still is not being used the thermal fluid temperature will rise. The signal from TE300 will
be used to detect this condition and the control system turns off the call for heat signal to the flame programmer as
previously described. As long as the thermal fluid temperature is sufficient to maintain the selected drying
temperature the heater will remain in this state. If the thermal fluid temperature must be increased to maintain the
proper air drying temperature, the signal from TE300 will be used by the control system to apply the call for heat
signal to the flame programmer. Temperature switch (TS300) continuously monitors the thermal fluid temperature to
ensure that the thermal fluid does not overheat. If the thermal fluid temperature exceeds the specified limit the switch
will open the flame programmer interlock circuit to stop heater operation. Alarm signals will also be provided to the
control system by the flame programmer and temperature switch.
The expansion tank contains a dip stick to periodically check the thermal fluid level in the tank. The dipstick has
marks indicating when thermal fluid needs to added and when the expansion tank is full.
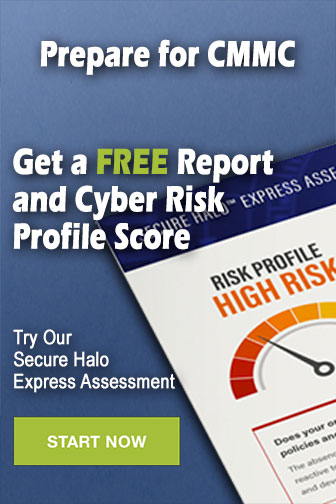