TM 10--3510--221--24
0006 00--1
AIR SYSTEM THEORY
OF OPERATION
0006 00
AIR SYSTEM
The air system provides dry compressed air to the other LADs systems. This air is used to pressurize the air bags
that support the drums and to actuate ball valves, air dampers, drum brakes, and door locks used on the
washing/drying system and water recycle system. A small amount of air is also used to detect the water level in the
wash tanks, rinse tanks, still, and stand pipe. Air system operation consists of the following sub--operations.
AIR COMPRESSION AND CONDITIONING
Ambient air enters the air system through an inlet filter. The inlet filter is used to prevent debris (sand, dirt, leaves,
etc...) from entering the air compressor (M500). The air compressor is used to pressurize the air entering the system
from atmospheric pressure to approximately 125 psig. The compressor is a two--stage, two--cylinder, reciprocating
piston type that is driven by an electric motor. A relief valve is mounted at the compressor outlet to prevent the
discharge pressure from exceeding safe limits. Air leaving the compressor is routed to a coalescing filter that
removes most of the water generated during the compression process from the product air. The filter contains a
disposable element that separates particles and water from the air. A float valve located in the filter bowl
automatically drains the filter to remove the separated water. Once the air leaves the coalescing filter it passes
through a dehydrator. The dehydrator is used to completely dry the product air. The dehydrator consists of two
vessels packed with desiccant, a solenoid valve, and a timer. While product air is being dried in one vessel, a small
amount of air is being used to purge water from the other vessel. Approximately every thirty seconds, the timer
signals the solenoid valve to change positions, this allows the product air to be routed through the vessel that was just
purged while the other vessel is being purged of water.
COMPRESSED AIR STORAGE
When the air leaves the dehydrator it is stored in the air tank. When the tank is fully pressurized it contains enough air
to allow the compressor to operate intermittently (approximately 20 minutes per hour) while still allowing smooth
operation of the air--driven components. Pressure sensor (PT500), mounted on the air tank, is used to determine
when the compressor should turn on and off. When the pressure in the tank drops to 85 psig, due to operation of air
driven components, the signal sent to the control system by the sensor will prompt the control system to turn on the
compressor. Likewise, when the air tank has been recharged to the proper pressure the signal from the sensor will
turn off the compressor. A relief valve is mounted on the air tank to prevent the pressure of the stored air from
exceeding safe limits. The air tank also contains a manual valve to allow the tank to be de--pressurized prior to
performing maintenance on the air system. A check valve is provided at the tank inlet to prevent pressure in the air
tank from bleeding back through the dehydrator when the compressor is not operating.
PRODUCT AIR DISTRIBUTION
A pressure regulator is used to control the pressure of the air delivered to the air driven components. The regulator is
set to deliver air at 80 psig regardless of normal changes in flow demand. The regulator is adjustable and contains a
pressure gauge (PI500) that indicates the regulated pressure. Pressure sensor (PT501) is also mounted at the outlet
of the pressure regulator. This sensor is used by the control system to verify that sufficient air pressure is available to
operate the air driven components. Product air leaving the pressure regulator is distributed to the solenoid manifolds,
orifice manifold, and drum air bags. Four solenoid manifolds, each consisting of eight 4--way valves, are provided to
control operation of the various air--actuated ball valves, air dampers, drum brakes and door locks. These 4--way
valves use electrical signals received from the control system to control the direction of air flow to and from the air
driven components. The orifice manifold is used to control the flow of air to the tank level sensors.
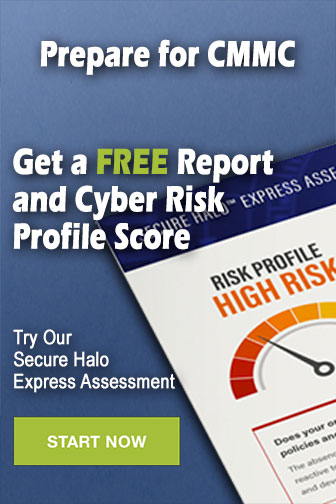