TM 10-8400-203-23
Change 10 26-9
Section II. MAINTENANCE PROCEDURES
Materials used to repair the ACVC shall be serviceable materials recovered from similar, salvaged or new
materials that conform to the specifications listed in Section III.
Serviceability classification for the ACVC Components shall be determined in accordance with Chapter 1.
Prior to repair of the ACVC, all components must be removed and cleaned. Disassemble the ACVC as
described in paragraph 26-8, Repair. Remove batteries from the battery box before cleaning.
Clean the helmet shell with soap and warm water. Rinse with clean water. Clean the synthetic rubber edging of
the shell with a clean cloth to remove dirt, dust, oil, grease, and perspiration.
Ensure that all communication components such as: cords, microphone, microphone boom, connectors, and
ear pads are free of any dirt or contamination. Remove loose dirt with a clean, soft cloth damped with a mild
detergent solution. Remove grease, fungus, or difficult to remove dirt, with a soft brush and mild detergent.
Hand wash camouflage cover in warm water (1200F) and mild laundry detergent or machine wash on
permanent press cycle. Rinse thoroughly with clean warm water after laundering. Hang and let air-dry.
Clean the Helmet Liner Assembly Components as necessary by removing and washing the components with a
mild solution of detergent and water. Air dry after washing.
Inspect the helmet shell for cleanliness, cracks, cuts, deep gouges and delimitation. Check the hook fastener
strips for serviceability. Inspect the rubber edging to see that there are no cuts and that the edgings are
securely adhered to the helmet shell. For the helmet shell, all inspection, cleaning, and maintenance will be
done in accordance with TM 10-8400-203-23, Chapter 19.
Inspect the camouflage cover for tears, and loose or missing fastener strips. Also check for broken stitching.
Inspect the impact liner assembly inserts for tears, cuts, filth, bad odor, soft spots, and improper adhesion of
components. Soft spots can be detected by compressing the inserts with fingertip.
Check the retention system for proper closure operation of the chinstrap. Check for cuts, tears or broken
stitching in the polyaramid cloth. Check for serviceability on the hook and pile fastener strips in the nape strap.
Inspect the headset assembly for physical damage such as abrasion, cuts, loose wires and connectors in the
microphone and earphones. Inspect all swivel joints and moveable parts. Check for foreign matter stuck in the
microphone.
Inspect the headset-microphone set for cleanness, cracks, loose switch, and loose or broken electrical lines
and connections. Be certain that the ear seals are properly installed on the ear cups.
Inspect all openings in the microphone and earphones. Inspect all swivel joints and moveable parts. Remove
all foreign matter, but do not use a pointed tool. Be careful not to puncture ear-cushioning seals. The assembly
is built to withstand breakage under normal and even abnormal operating conditions. Routine maintenance
involves replacing damaged earcup seals and batteries for the talk-through system, as needed.
26-4. MATERIALS
26-5. CLASSIFICATION
26-6. CLEANING
26-7. INSPECTION
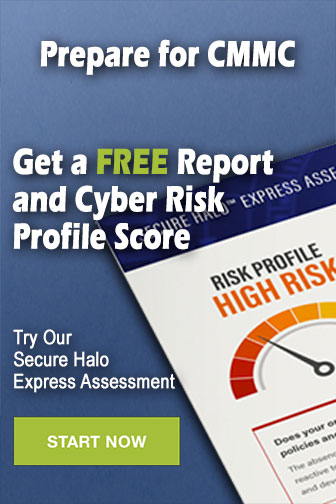