TM 10-3510-222-24
Section III. GENERAL MAINTENANCE PROCEDURES
4-5. GENERAL.
The procedures in this section have been arranged in order in which the items appear in the General Support (H)
Maintenance level column on the Maintenance Allocation Chart (MAC) which is provided in Appendix B. Step by step
procedures have been provided for all actions authorized to be performed by Unit, Direct Support Maintenance in
Chapters 2 and 3, and General Support in Chapter 4.
WARNING
High voltage is present on this equipment. Do not perform maintenance with power on. Death or
serious injury to personnel may result.
a.
Wiring
(1)
General. Preferred repair methods consist of replacing wires, terminals, connectors, etc., rather than splicing
wires, bending ends to form terminals, and other makeshift procedures, although the latter may be
appropriate for emergency field repairs. Determine the proper size and length of wire, or the terminal, or
connector to be used for replacement by referring to Appendix F. Cable Diagrams, Wire Run List, and
Control Circuits.
(2)
Soldering Connections. Wire connections must be made mechanically sound before they are soldered.
Solder alone does not provide sufficient strength to prevent breakage. Joining surfaces of connections to be
soldered must be clean and bright. If a separate flux is used, it should be rosin base flux and should be
brushed onto the joint before soldering. If a flux-core solder is used, it should be a rosin core electrical
solder. If uncored solder is used, it should be a lead-tin solder. Wires should always be heated to the point
at which the solder will melt completely and flow into all parts of the joint. Excessive build up of solder
"gobs" on the joint should be avoided or removed.
(3)
Insulating Joints. The preferred method of insulating electrical joints is by the use of heat-shrink tubing. To
apply, cut a piece of heat-shrink tubing of suitable diameter to a one-inch length for covering joints at
terminals or connectors, or to a length about 1/2 inch (1.3 cm) longer than the joint to be insulated, and slide
the tubing over the wire before making the joint. After the joint is made, slide the tubing so that it covers the
joint, and shrink in place with moderate heat.
(4)
Splicing Wires. To repair broken or cut wires that are otherwise sound, the mating ends can be stripped and
spliced. A commercial butt splice can be crimped onto the ends to join them, or a "Western Union" wire
splice can be made. The latter is made by stripping 1/4-1/2 inch (6.5-12.7 mm) of insulation from the wire
ends, holding the ends parallel and facing opposite directions, then twisting each end around the other wire at
least three turns. Solder and apply insulation as described above.
(5)
Crimping Terminals. To install a terminal on the end of a wire, strip 1/4 - 1/2 inch (6.5 - 12.7 mm) of
insulation from the end of the wire, apply a one-inch piece of heat-shrinking tubing (if the terminals are of the
uninsulated type) and insert wire end into the shank of the terminal. Crimp the shank, and install heat-shrink
tubing, if necessary.
4-3
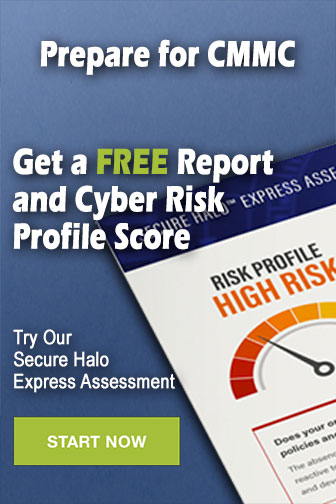