TM 10-8400-203-23
3-5. REPAIR AND MAINTENANCE OF BODY ARMORContinued
(2)
(3)
(4)
(5)
When replacing the vinyl casing, remove the ballistic insert from old casing. If the ballistic insert (after
examination) is found to be dry, not damaged, and contains stiffeners, place it into a new casing,
insuring that the ballistic insert lies flat and unbunched in the casing and that the collar is inside the
casing collar. Force excess air out of the casing then heat seal the bottom opening of the vinyl casing
to form a water tight closure.
Heat sealing of vinyl casing. Insure that ballistic insert is properly positioned in the vinyl casing; force
excess air out of casing: smooth the bottom open end so as to be free of wrinkles or folds, and seal the
end in the dielectric heat sealer platens. The closing seal shall be not more than 3/8 inch (0.953 cm)
from the end. Care should be taken in the sealing operation that no loose threads, fuzz, or any other
foreign matter is in the area to be heat sealed. The heat seal on the end should intersect and cross
both of the side heat seal areas. The closing seal shall be obtained in accordance with good heat
sealing practice to produce a seam of equal strength to that of the side seams. It is recommended
prior to each production run that machine settings be checked on a vinyl casing by performing at least
three or four trials to insure an adequate seal.
Heat sealing of vinyl casings by hand. Perform hand sealing in the same way as described above
except as follows:
(a)
(b)
(c)
(d)
(e)
(f)
(9)
(h)
An electric hand sealing iron (para 3-11) shall be used.
The sealer shall be set at its maximum high setting.
The heat sealing shall be done on a smooth wooden or hardboard surface.
The wooden or hardboard working surface shall be covered in the heat sealing area with a 5 MIL
teflon film to prevent sticking of the film to the surface when sealing. Alternatively, the heat sealing
area may be covered with silicone coated release paper, coated side up.
The envelope open end to be heat sealed shall be placed on the working surface, smoothed out,
and covered by a transparent or translucent ironing film (5 MIL thick teflon (sec Ill) ). The ironing
film allows the operator to see whether thorough fusion of the two layers of vinyl casing has taken
place along the entire closure.
The sealing shall be aided by the use of a guide, such as 1/4 inch (0.635 cm) thick steel bar stock,
along which the sealing iron shall be drawn. The sealing iron shall be tilted approximately 20° so
that the sealing is done by the edge of the sole plate only, to produce a seal line between 1/16-to
3/16-inch (0.159 to 0.476 cm) wide.
The sealing shall be conducted at an approximate rate of one inch per second.
After sealing, allow several seconds of cooling to take place, then peel off the ironing film slowly.
After heat sealing, place the casing with ballistic insert into the nylon outer cover. Fold the excess
bottom length of the vinyl casing under and stitch the end of the outer shell, taking care that the
stitching does not pass through any portion of the vinyl casing,
3-11
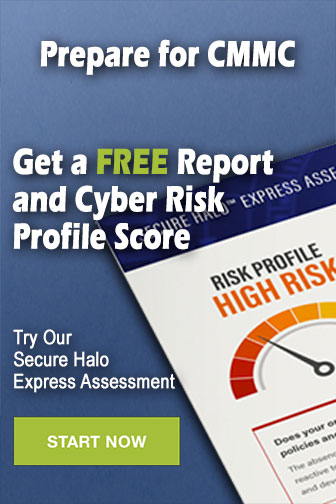