TM 55-1615-226-40
Figure
And
Part No.
Nomenclature
Test
Longitudinal
Circular
Index
(With Coil DC)
(With Heads DC)
Number
45.
204-011-408 Collective
M
10,000 Amp Turns*
2,000 Amps-1-l/2°
Sleeve
Use two shots for
Central Conductor
complete coverage.
TEST CODE
M = Magnetic Particle Inspection Per MIL-I-6868
F = Fluorescent Penetrant Inspection Per MIL-I-6866
NOTE
Divide Amp turns specified by number of turns in coil of equipment used, to
determine amperage to be applied to part.
2-17. Scissors Assembly.
2-18. Inspect scissors assembly as follows:
CAUTION
Take necessary precau-
tion to protect any
bearings not removed
from assembly, from
contamination
by
penetrant during non-
destructive inspection
test.
a. Perform nondestructive inspection in accor-
dance with table 2-1.
b. Inspect inner race (26, figure 2-1) for flaked or
spalled area, brinelling, wear bands, scratches, or
defects on contact surface.
c. Inspect bearings (27 and 29) for dented seals or
shields, broken, cracked or spalled, flaked, pitted,
scored, etched areas, rust or corrosion, wear bands on
rollers, or excessive looseness due to wear.
d. Inspect bearings for evidence of overheating.
NOTE
Light gray lubrication
stains are acceptable,
provided the surface is not
physically affected.
e. Inspect thrust washer (25) for wear or damage.
f. Inspect housing (23) and seal (71X6223) (24) for
wear and damage.
g. Inspect spacers (18 and 19, figure 2-1) for wear
and damage, pitting, scratches, rust corrosion, and
cracks.
h. Visually inspect spacer (28, figure 2-1) in scis-
sors for damage.
i. Inspect bearing set (20) for damaged seals or
shields, smoothness and freedom of operation, and
excessive looseness of bearings, end liner (19) for
wear and damage.
j. Inspect bearings (49 and 51) for freedom of
movement and smoothness of operation. Inspect
bearing (49) and liner for looseness. Any looseness
will require removal of liner and checking bearing
(46). Egging of the hole not to exceed 0.001 for 30
degrees. Inspect bearing (51) and liner (50) for loose-
ness. Any looseness will require removal of the liner
(50) and checking the mating hole. Egging shall not
exceed 0.0005 for 30 degrees.
k.. Inspect scissors (6) for mechanical or corrosion
damage.
(1) Mechanical damage must not exceed 0.010
inch in depth in area from the centerline of the pivot
bore to the extremity of the drive link attachment lug.
This damage is not to violate minimum dimension
shown in figure 2-1.1.
(2) Corrosion damage must not exceed 0.005
inch in depth from the centerline of the pivot bore to
the extremity of the drive attachment lug. This
damage is not to violate minimum dimension shown
in figure 2-1.1.
(3) Mechanical damage to surfaces within 0.5
inch of any hole must not exceed 0,010 inch in depth
from the centerline of the pivot bore to the extremity
at the drive link attachment lug, and repair area
must not exceed 25 percent of the area within 0.5 inch
of any hole.
(4) Corrosion damage to surfaces within 0.5
inch of any hole must not exceed 0.005 inch in depth
from the centerline of the pivot bore to the extremity
of the drive link attachment lug, and repair area
must not exceed 25 percent of the area within 0.5 inch
at any hole.
(5) Mechanical damage must not exceed 0.035
inch in depth in all areas of scissors other than
specfied in (1) and (3) above,
(6) Corrosion damage must not exceed 0.017
inch in depth in all other areas of scissors other than
specified in steps (2) and (4) above.
(7) Mechanical or corrosion damage in any one
erea must not exceed 0.25 square inch in area or 0.75
inch in any one length.
Change 4 2-5 2-5
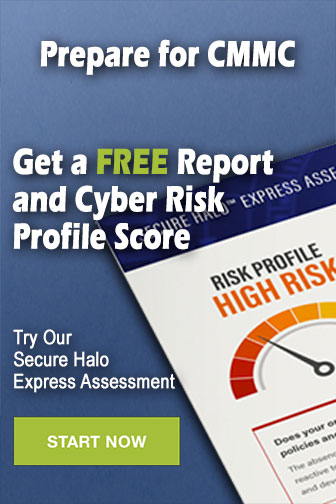