TM 10-1670-300-20&P
TO 14D1-2-469-2
NAVAIR 13-1-42
3. Cloth. Inspect for breaks, burns, cuts, frays, holes, rips, snags, tears; loose, missing, or
broken stitching or tacking; weak spots, wear, or deterioration.
4. Fabric Tape, Webbing, and Cordage. Inspect for breaks, burns, cuts, frays, holes,
snags, tears, incorrect weaving, and sharp edges formed from searing, loose, missing,
or broken stitching, tacking, shipping, and weaving; weak spots, wear, and deterioration.
5. Pressure-sensitive (adhesive) Tape. Inspect for burns, holes, cuts, tears, weak spots;
looseness and deterioration.
6. Rubber and Elastic. Inspect for burns, cuts, holes, tears, weak spots; loss of elasticity
and deterioration.
7. Felt. Inspect for cuts, tears, burns, breaks, holes, and thin spots.
8. Leather. Inspect for burns, cuts, holes, tears, loose missing or broken stitching; thin
spots and deterioration.
c.
In-Storage Inspection.
(1) An in-storage inspection is a physical check conducted on a random sample of air delivery
equipment which is located in storage. The purpose of the inspection is to ensure that the item is ready for
issue, that the item is properly identified and segregated from other types of equipment, that no damage or
deterioration of the equipment has taken place, and that all modification work orders (MWO) have been
completed. The inspection shall also concern the methods of storage of air delivery items, the adequacy of
storage facilities, efforts of pest and rodent control, and protection from unfavorable climatic conditions.
(2) Air delivery equipment which is in storage will be inspected at least semiannually and at more
frequent intervals if prescribed by the local parachute maintenance officer. The frequency of inspection
may vary according to the type of storage facilities and local climatic conditions.
(3) In-storage inspection will be conducted only by parachute rigger designated by local parachute
maintenance officer.
d.
Salt-Water Contamination Test. To test for possible salt water contamination, lay the item out on a
suitable surface and look for a white crystalline residue.
d.
Equipment Disposition. Air delivery equipment may be rendered unserviceable by either normal fair
wear or by aging and will subsequently be repaired, modified, or condemned, as appropriate. Equipment that is
uneconomically repairable (outdated) will be condemned. Disposition of air delivery equipment that is
condemned, unserviceable, or for which serviceability is uncertain, will be accomplished using the following
procedures as applicable:
(1) An air delivery item which requires repair or modification will be tagged in accordance with DA
Pam 738-751. Subsequent work will be performed on the item at the maintenance level specified for the
maintenance function on the MAC, Appendix B, Section II of the manual.
(2) Disposition of Condemned Air Delivery Equipment. Condemned equipment, other than being
involved in a fatality, will be removed from service and disposed in accordance with current directives
listed in Appendix A of this manual.
2-15
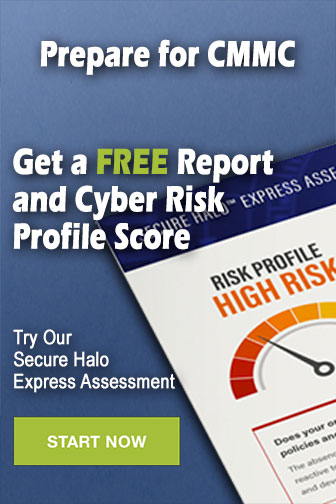